Electron Beam Weld
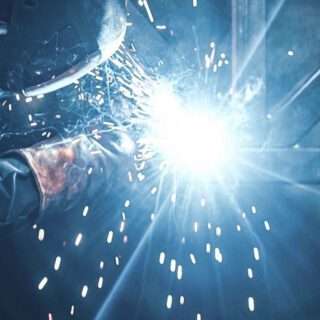
The Electron Beam Welding (EBW) process employed by MIC Group leverages a high-energy electron beam that is directed with great precision to melt and fuse materials at the points where they join. This method ensures that the resultant welds exhibit not only exceptional strength but also maintain the overall structural integrity of the materials being worked on. This advanced technique stands out because it creates a minimal Heat Affected Zone (HAZ), which is a crucial factor in welding, as it helps to reduce the risk of thermal distortion. Consequently, this preservation of the mechanical properties of the base materials is of utmost importance to ensure quality and performance. Additionally, to enhance the effectiveness of the welding process, EBW is conducted within a controlled vacuum atmosphere. This carefully regulated environment plays a vital role in eliminating any potential impurities that might affect the weld quality, thereby guaranteeing a clean, high-quality weld that meets stringent standards.
One of the significant advantages of Electron Beam Welding, often referred to as EBW, is its remarkable capability to achieve deep penetration with a narrow fusion zone. This characteristic makes EBW particularly suitable for applications that demand high precision, repeatability, and superior strength. The ability to focus the energy into a small area allows for controlled thermal input, which is crucial for maintaining the integrity of the materials being joined. Additionally, EBW provides the unique advantage of enabling the joining of dissimilar metals, which broadens the possibilities for design and engineering in various fields. This capability is especially valuable in industries such as aerospace, defense, power generation, and industrial applications, where the integration of different materials can lead to innovative solutions and improved performance.
Benefits of Electron Beam Welding:
This process creates strong and precise welds that significantly enhance the integrity of the joint while ensuring that there is minimal impact on the surrounding material. The welding technique utilized ensures that heat is applied effectively, leading to deep penetration into the base materials, which results in a robust connection. Additionally, the careful control of heat minimizes distortion in the surrounding areas of the weld, preserving the overall geometry and quality of the parts being joined. This combination of deep penetration and minimal distortion is crucial in various applications where structural integrity and dimensional accuracy are essential.
The concept of a Narrow Heat Affected Zone, commonly referred to as HAZ, plays a crucial role in maintaining the integrity of materials during processes such as welding or machining. By ensuring that the heat generated during these processes is kept to a minimum, the HAZ can significantly preserve the material properties of the surrounding area. This preservation is vital as it leads to enhanced strength and durability of the overall material. As a result, engineers and manufacturers can achieve better performance and longevity in their products by carefully managing the HAZ during operations.
In our operations, we ensure that the welding processes we utilize exhibit a high degree of precision and repeatability. This means that every time we perform a weld, we do so with a level of accuracy that guarantees the final product meets the exact quality standards we have set. By maintaining such consistency in our welding practices, we are able to deliver products that not only meet but often exceed our clients’ expectations, thereby reinforcing our commitment to high-quality output and customer satisfaction.
The process of eliminating impurities is conducted in a vacuum environment, which is essential for maintaining the integrity of the materials involved. By carrying out this procedure in a controlled vacuum setting, we effectively prevent any potential contamination that could arise from external sources. This careful approach ensures that the purity of the materials is preserved throughout the elimination process, leading to more reliable and high-quality outcomes.
By eliminating the need for any filler material, this approach significantly lowers costs associated with additional materials. It also enhances the overall quality of the weld, leading to a more pure and consistent result. This improvement in weld purity is particularly beneficial for industries where the integrity of the weld is critical to the performance and safety of the final product.
When it comes to needing high-precision and high-strength welding solutions, you can rely on MIC Group’s Electron Beam Welding to provide you with the best in the industry. This advanced welding technology offers unmatched quality that meets stringent specifications, ensuring that you receive results that are not only efficient but also highly reliable. This makes it particularly suitable for even the most demanding applications across various sectors, where the integrity and durability of welds are of utmost importance.
MIC Group offers customized, innovative solutions that ensure exceptional quality and efficiency. Click the button below to download a summary of MIC Group’s services and capabilities.
Related Articles
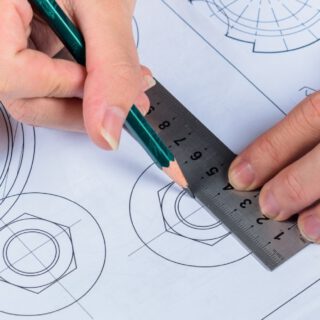
5 Ways MIC Delivers Value Beyond Manufacturing
5 Ways MIC Delivers Value Beyond Manufacturing In today’s fast-paced world, businesses need more than
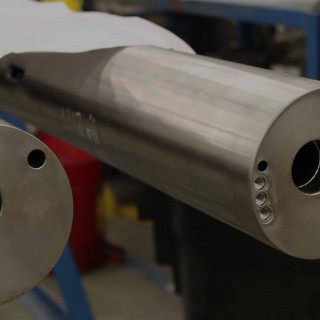
Advanced Machining and Assembly Solutions with MIC
These services are made to solve even the toughest manufacturing challenges that businesses face today.
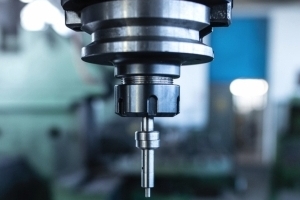
Making the Complex Simple – MIC’s Expertise in Manufacturing Solutions
60 years of experience, MIC Group transforms manufacturing complexities into efficient solutions.
Request More Information
Learn more about the Engineering Design services offered by MIC